Software Heidenhain Serial Cable
Schematic of PC - Heidenhain Controller Serial. Title: PC-Heid.PDF Author: Bemphill Subject: PC-Heidenhain Serial Cable Keywords: Heidenhain, serial, cable, RS-232. Chapter 9 Data Transfer: PC. The following procedures have been written to reflect the PC hardware and software. Ensure the PC-Heidenhain Serial Communications.
Afternoon chaps, Newbie here - new, that is, to CAD, CAM and CNCing. I've been machining for a couple of years, had my CNC mill a few months, and I'm just started to get to grips with it all. I've been searching for a suitable CAM program, and CamBam looks like it's going to be it.
Here's the thing, though; My machine is an elderly Bridgeport Interact 1 Mk2, with a TNC151 controller. I managed to get it to go into ISO mode, loaded a simple drawing into CamBam, and used the post-processor & script posted elsewhere on this very forum. Unfortunately, the resulting NC simply crashed my processor, after looping around the first three instructions a few times. Not to be disheartened, I switched back to conversational (which I have been learning via the HH manuals); re-did the TNC151 post-processor to output HH Conversational commands, and modified the script to fix up the various issues the postprocessor can't do/leaves behind. I've used this PP + script to generate a fairly simple machining sequence. I haven't tried the drilling canned cycle yet, and may need to amend that bit. I also seem to get a lot of errors in CamBam, but the resulting code is fine?
Not sure what's happening there, any clues welcomed. I'd really appreciate it if anyone else running a similarly old HH control in conversational mode could try it out & let me know if they get snags. Hopefully, I'll be able to do the same too. Meantime, a BIG thank you to jmccracken, lloydsp and others for the work they put into the G-code version, without that I would have been struggling big time. PS: To use the post-post processor script, copy the H-151-C Post-Post.txt file to your c: drive & change the extension to.vbs EDIT: The old version of this postproc didn't work very well; attached now is the latest version as of 14/mar/2013, which works much better.
What a beneficial coincidence! I have been playing with Cambam for 3 or 4 years now using my homemade Axminster XY table plus cobbled up Z axis. It has produced some brilliant work for my traction engine model. However, last week a friend in real engineering has sold me an Interact 1 mk2 all in original and working condition. I notice it can accept G codes and was hoping to get Cambam to oblige so as to save learning HH and now here you are with a solution! It is going to take me a week or so to get the machine installed and powered up but I will report progress as soon as I get some! Regards, Les Logged.
Thanks Lloyd, Since posting here I found a link to CNCzone with info about a similar issue. The poster, Jmccracken, sorted his machine out and listed a full set of settings. I checked all my settings and altered them to his but sadly no result. I too am using the Heidenhain TNC Server program via a serial port on my PC. Les Here is my current set-up copied from CNCzone:- 'I wanted to try to give a definitive guide to setting up drip-feeding a Heidenhain 151B based on my (epic) saga of the last few days. I can't say that there aren't other ways to make this work, but the following steps work on my machine.'
Communications pertinent machine parameter M71: 515 MP218: 17736 MP219: 16712 MP220: 279 MP221: 5382 MP222: 168 MP223: 1 MP224: 4 2. Cable between PC (9-pin serial / DB9) and Heidenhain 151B controller (25-pin serial / DB25). This equates to a DB9-DB25 null modem cable.
(25pin TNC) - (2) - (3) - (4) - (5) - (6) - (7) - (20) - 3. Install TNCServer from Heidenhain website. Setup TNCServer to 'FE' mode and 9600bps (baud). See attached screenshots: 4. Press the MOD key on the Heidenhain 151B controller. By pressing the up or down arrow, find 'RS-232-C-INTERFACE' and set it to 'FE' mode. See attached screenshot: 5.
While still in the MOD menu, press the up or down arrow, find 'BAUD RATE'. On my controller, my only choice was 2400. Leave it or set it to 2400.

Note that this is the non-sequitur. And what took me so long to figure out (specifically that the Heidenhain controller is set to 2400 baud while TNCServer is set to 9600 baud). WTF, one might ask.
Turn on the PC and connect to the Heidenhain 151B controller which is in any normal operating mode (manual, automatic run, etc.). TNCServer should say 'Ready' in the bottom left corner. In TNCServer, set the 'folder' to the correct folder having your programs. Note that ISO programs (what I'm using) have to be named the 'program number' 'I'. In this case, program number '1' must be a text file named '1.I'. I'm told that Heidenhain programming language uses 'program number' 'H'.
Les, Let's take this boat in as simple a course as possible. You noted a discrepancy, so I wonder - did you try setting the TNCserver to 2400 baud, since that appears to be all your machine will accept? Also, if you have schematics or a user manual for the Heidenhain, it might be worthwhile to check the pinouts on the RS232 connection. It's reasonable that the mill would be DTE (data terminal equipment), since often they were fed from modems or RS232 multiplexers, but it bears checking. Your PC IS DTE, which is why one should need a null-modem to communicate with it. If the mill is DCE (data communications equipment), you need a 'straight-through' cable, which reverses 2&3, and re-assigns the various flow-control pins.
Let's hope that's not necessary. Without some specifics on the mill, I couldn't advise you correctly. However, below I'll offer a hint as to how to check the connector to see if it's correct, at least for pins 2&3 (if you have a voltmeter). If that did not help, then the first thing you should do is break out your copy of Hyperterm.
Serial Cable Connection
It is usually included as an accessory under XP. 'All programs/accessories/communications/Hyperterm' Connect your RS232 cable to your PC, but NOT to the Heidenhain. When you first run Hyperterm: 1) Select an icon, and a name for this new connection. 2) Under 'connect to', ignore all fields except the 'connect using' field. You should select the COM port you're intending to use on your PC. 3) Under 'port settings', select 2400, 8, none, 1, and 'none' for flow-control (this may have to change to 'hardware' or 'Xon/Xoff' for the mill, but its software should set that automatically, if it's not a user setting). Click 'apply' to make the settings stick, then 'OK' to exit the setup menus.
Check under 'File/Properties/Settings/Ascii Setup' to make sure that 'echo typed characters locally' is NOT checked. Type a few random characters. You should see nothing new appear on your screen.
Now, using a means that ensures you do not short anything else together, shunt pins 2 & 3 of the end connector on your RS232 cable. Any conductive tool will work - just be certain you do not short those two pins to the shell or any other pin.
While shunted, type again on the keyboard. You should see the characters echoed to the screen. If this does not work, your port number is wrong, the port is non-functional, or the cable is defective.
To try another COM port (if there is one), use 'Call/Disconnect' to terminate the connnection. Then use 'File/Properties/Connect To/Connect Using' to select a different COM port. If it does work, you may try other baud rates, simply to make sure your cable and port are capable of handling higher speeds. To do this, use 'call/disconnect' to terminate the connection to your COM port. You may then use 'File/Properties/Connect To/Configure' to set new baud rates. At this point, I suggest you leave it set to 2400 baud, and connect the cable to the mill, and try everything again.
That's the end of checking your PC's end. Without knowlege of the Heidenhain protocols, I cannot tell you more about it. You can check the connectors for a crude determination that they are right by looking at the voltages on pins 2 and 3 of each connector. With only the PC end of the cable connected, and a connection established on the PC with Hyperterm, you should see a voltage of about -5VDC on pin 3, referenced to pin 5 as ground. With only the mill connected, and looking again at the pc-end connector, you should now see a voltage of about zero volts on pin 3, but a negative voltage of from -5 to -15 volts on pin 2 (again referenced from pin 5 as ground).
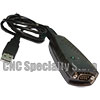
Serial Cable Bulk
If those two conditions exist, you definitely have pins 2 and 3 of the respective ends hooked up correctly. The flow control pins can get more difficult to ascertain, since they don't have defined static conditions unless the software is under control at both ends. At least, you must have the PC and mill running at the same baud rate. So that's a start. Lloyd Logged. An update on my Intereact progress:- I have the machine fully up and running.
So far the only damaged/worn part has been the Y axiz gib strip. There was so much slack you could shake the saddle a quarter of an inch each way. Amazingly, only the gib was worn, not the dovetails. So I reground both sides of the gib and put it back in with a 25 thou shim behind it an it now adjusts up to the tolerance in the manual. I have used Ade's post processor very successfully on ordinary profile work and have just completed a lengthy engraving sequence, all perfectly converted. However, the problems started when I tried to PP a drilling operation. The PP will not successfully convert a drilling sequence.
Null Modem Serial Cable
As I don't yet know how to program a drilling sequence in HH to compare it with, I am now spending some time trying to get to grips with HH. Thanks Lloyd, All I was trying to do was drill two holes, 40mm either side of centre on the x axis.